Maximizing Desander Cone Performance in Elevated Temperature Environments
May 04,2025
Maximizing Desander Cone Performance in Elevated Temperature Environments
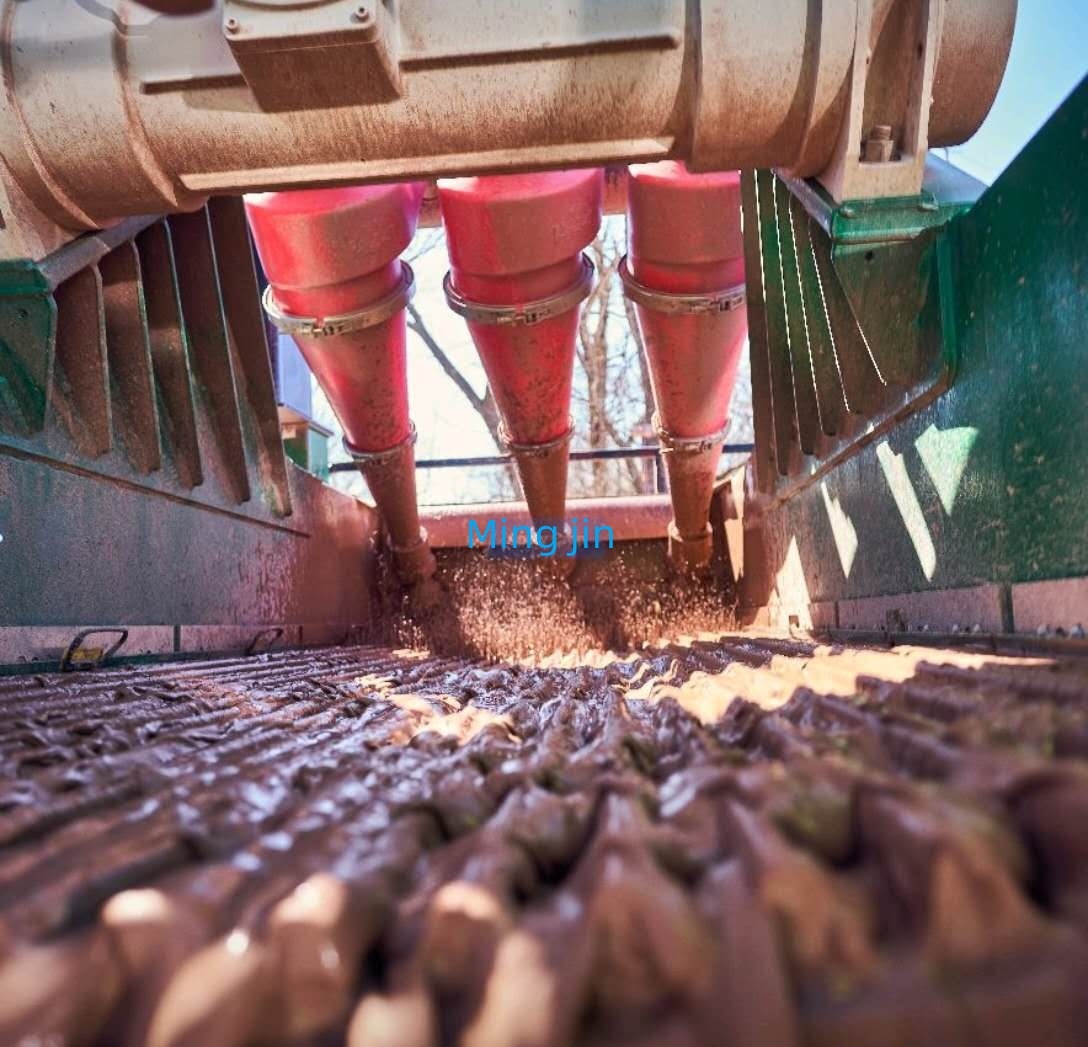
Maximizing Desander Cone Performance in Elevated Temperature Environments
The oil and gas industry often operates in challenging environments, where elevated temperatures can significantly impact equipment performance. One crucial component in this context is the desander cone, which plays a vital role in separating solids from liquids in drilling fluids. Optimizing the performance of desander cones in high-temperature environments is essential for maintaining operational efficiency and prolonging equipment lifespan. This article will explore the factors influencing desander cone performance under elevated temperature conditions and provide strategies for maximizing efficiency.
Understanding Desander Cone Functionality
Desander cones are designed to remove larger solids from drilling fluids, thereby preventing wear and tear on pumps and other downstream equipment. The operational principle relies on the centrifugal force generated by the fluid's velocity as it enters the cone. In high-temperature environments, the properties of the drilling fluid can change, affecting the desander's efficiency. Elevated temperatures can lead to increased viscosity, altered fluid density, and reduced sedimentation rates, all of which can hinder the desander's performance.
Impact of Elevated Temperatures on Drilling Fluids
One of the primary challenges in high-temperature environments is the behavior of the drilling fluid. As temperature increases, the viscosity of the fluid may rise, making it more challenging for solids to settle out. This change can lead to an increase in the concentration of solids in the drilling fluid, which can overwhelm the desander cone. Additionally, higher temperatures can accelerate the degradation of certain additives used in the drilling fluid, further complicating the separation process.
To address these challenges, it is crucial to select drilling fluids that are specifically formulated for high-temperature applications. These fluids often contain specialized additives that enhance performance at elevated temperatures, helping to maintain optimal viscosity and fluid density.
Optimizing Desander Cone Design
The design of the desander cone itself can also play a significant role in its performance under high-temperature conditions. Several factors should be considered when optimizing desander cone design for elevated temperatures:
1. Material Selection**: The materials used in the construction of the desander cone must be capable of withstanding high temperatures without compromising structural integrity. Materials such as high-grade stainless steel or specialized alloys can provide the necessary durability.
2. Cone Angle and Size**: The angle and size of the cone can significantly impact the centrifugal force generated during operation. A steeper cone angle may improve separation efficiency by increasing the velocity of the fluid, while larger cone sizes can accommodate higher flow rates.
3. Flow Rate Management**: Maintaining optimal flow rates is crucial for maximizing desander performance. Excessive flow rates can lead to turbulent flow conditions, reducing the efficiency of solid separation. Implementing flow rate control systems can help maintain optimal conditions for the desander cone.
Regular Maintenance and Monitoring
To ensure optimal performance of desander cones in elevated temperature environments, regular maintenance and monitoring are essential. Over time, wear and tear can affect the cone's efficiency, leading to reduced performance. Implementing a proactive maintenance schedule can help identify potential issues before they become critical.
Training and Best Practices for Operators
In addition to equipment optimization, the training of personnel operating desander cones is crucial for maximizing performance in high-temperature environments. Operators should be well-versed in the specific challenges posed by elevated temperatures and equipped with the knowledge to implement best practices.
Best practices may include:
Understanding Fluid Properties: Operators should be trained to understand how temperature affects drilling fluid properties and how to adjust fluid formulations accordingly.
Monitoring Environmental Conditions: Keeping track of temperature fluctuations in the drilling environment can help operators anticipate changes in fluid behavior and adjust operations as needed.
Implementing Standard Operating Procedures (SOPs): Developing and following SOPs for desander operation can ensure consistency and efficiency, reducing the likelihood of operational errors.
Conclusion
Maximizing desander cone performance in elevated temperature environments requires a multifaceted approach that includes optimizing equipment design, selecting appropriate drilling fluids, and implementing regular maintenance and monitoring practices. By understanding the unique challenges posed by high temperatures and taking proactive measures, operators can enhance the efficiency and longevity of desander cones. This not only contributes to the overall success of drilling operations but also helps to reduce costs and minimize environmental impacts associated with drilling activities. As the oil and gas industry continues to evolve, focusing on equipment performance in challenging conditions will remain a key priority for achieving operational excellence.
Key words: