Understanding Hydrocyclone Filters for Efficient Slurry Separation in Chemical and Rubber Industries
Jul 13,2025
Hydrocyclone filters are specialized devices utilized for the efficient separation of solid materials from liquids in slurry mixtures. They operate on the principle of centrifugal force, which enables them to efficiently separate particles based on their size and density. This technology is particularly advantageous in industries such as chemical processing and rubber production, where slurry sepa
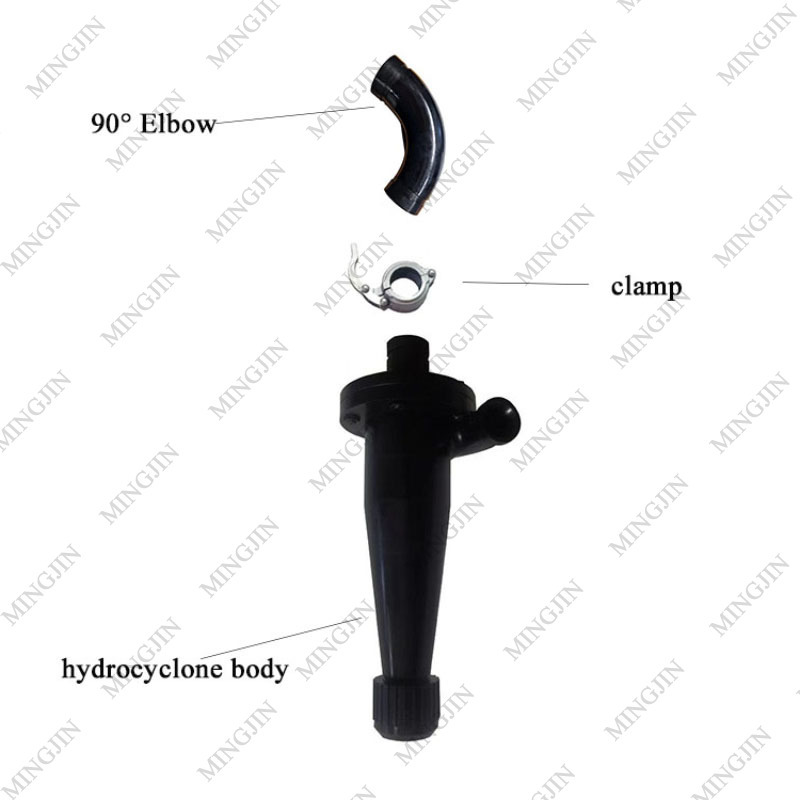
Hydrocyclone filters are specialized devices utilized for the efficient separation of solid materials from liquids in slurry mixtures. They operate on the principle of centrifugal force, which enables them to efficiently separate particles based on their size and density. This technology is particularly advantageous in industries such as chemical processing and rubber production, where slurry separation is a critical step in manufacturing and processing.
The working mechanism of a hydrocyclone filter is relatively straightforward. Slurry is introduced tangentially into the hydrocyclone, creating a vortex that causes denser particles to move outward while lighter particles remain closer to the center. As the slurry flows downwards, the denser particles are forced to the wall of the hydrocyclone, where they are collected and discharged through a designated outlet. The cleaner, less dense liquid is then allowed to exit through a separate outlet, resulting in effective separation.
One of the primary benefits of hydrocyclone filters is their ability to handle large volumes of slurry with minimal maintenance. These filters are designed to be robust and durable, making them suitable for heavy-duty applications. In the chemical and rubber industries, where consistency and reliability are paramount, hydrocyclone filters provide an efficient solution for maintaining product quality.
Additionally, hydrocyclones are energy-efficient devices that can reduce operational costs. They do not require moving parts, which minimizes energy consumption and maintenance needs. This is particularly beneficial in mass production settings, where continuous operation is necessary, and downtime can lead to significant financial losses.
Moreover, the use of hydrocyclone filters can enhance the overall quality of the final product. By effectively removing unwanted particles and impurities from the slurry, these filters ensure that the resulting materials meet stringent quality standards. This is essential in industries such as rubber manufacturing, where even minor contaminants can affect the performance and durability of the final products.
In summary, hydrocyclone filters play a vital role in the slurry separation process within the chemical and rubber industries. Their efficient operation, low maintenance requirements, and ability to enhance product quality make them an invaluable asset in modern manufacturing. Understanding the functionality and benefits of hydrocyclone filters can help industries optimize their processes and achieve better results in their production lines. By adopting such technologies, companies can ensure they remain competitive and deliver high-quality products to their customers.
The working mechanism of a hydrocyclone filter is relatively straightforward. Slurry is introduced tangentially into the hydrocyclone, creating a vortex that causes denser particles to move outward while lighter particles remain closer to the center. As the slurry flows downwards, the denser particles are forced to the wall of the hydrocyclone, where they are collected and discharged through a designated outlet. The cleaner, less dense liquid is then allowed to exit through a separate outlet, resulting in effective separation.
One of the primary benefits of hydrocyclone filters is their ability to handle large volumes of slurry with minimal maintenance. These filters are designed to be robust and durable, making them suitable for heavy-duty applications. In the chemical and rubber industries, where consistency and reliability are paramount, hydrocyclone filters provide an efficient solution for maintaining product quality.
Additionally, hydrocyclones are energy-efficient devices that can reduce operational costs. They do not require moving parts, which minimizes energy consumption and maintenance needs. This is particularly beneficial in mass production settings, where continuous operation is necessary, and downtime can lead to significant financial losses.
Moreover, the use of hydrocyclone filters can enhance the overall quality of the final product. By effectively removing unwanted particles and impurities from the slurry, these filters ensure that the resulting materials meet stringent quality standards. This is essential in industries such as rubber manufacturing, where even minor contaminants can affect the performance and durability of the final products.
In summary, hydrocyclone filters play a vital role in the slurry separation process within the chemical and rubber industries. Their efficient operation, low maintenance requirements, and ability to enhance product quality make them an invaluable asset in modern manufacturing. Understanding the functionality and benefits of hydrocyclone filters can help industries optimize their processes and achieve better results in their production lines. By adopting such technologies, companies can ensure they remain competitive and deliver high-quality products to their customers.
Key words: